In 1906 Mariani Packing Company was born when Paul Mariani emigrated from Yugoslavia to California with a dream to start his own business. He began by planting fruit trees on a small piece of land and over the years refined and perfected his knowledge of the growing areas. As the business grew and continued to thrive, Mariani began to contract with other growers to supply a greater variety of fruits. Then in the early 1940s, his son, Paul Jr., revolutionized the industry by introducing the first moist, ready-to-eat dried fruit packaged in ready-for-retail bags.
Mariani has always maintained close, personal relationships with their growers to ensure that they receive the highest quality fruit possible. Mariani also employs food technologists and lab technicians who maintain stringent quality control and adhere to strict HACCP guidelines. Today, under the leadership of Mark Mariani, CEO, and Paul’s great grandson, George Sousa Jr., President, Mariani has proved that their commitment to quality has helped them become the largest private dried fruit manufacturer in the world, selling 125 million pounds of product a year.
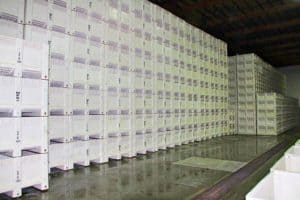
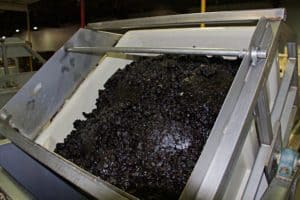
Improved Product Identification and Sanitization
Mariani’s growers pick premium fruit, then it is expertly inspected, washed, dried, and graded with state-of-the-art equipment. The dried fruit is then transported to the Mariani processing facility where it is transferred into bins. In the past, Mariani used wood bins during processing. Unfortunately with dark dried fruits, such as prunes, raisins, or cherries, there was not a lot of contrast between the color of the fruit and the inside of the wood bins. This made it very difficult to check the product for wood particles and other contaminants. In 2002, in order to improve their quality control, Mariani began the conversion from wood to the injection-molded plastic ProBin 24-S from Macro Plastics.
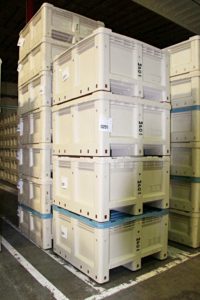
“Using ProBins has reduced our risk of product contamination from wood particles and the new secure- fitting MacroLids have further improved our product protection.” – Andy Kennedy, Production Manager, Mariani Packing Company
Because the materials used to manufacture ProBins are FDA-approved and splinter- resistant, Mariani is able to store and mix the dried fruit directly in the ProBins. The light color allows Mariani’s laser sorters to easily detect foreign materials or separate product that does not meet their quality standards. The smooth, nonporous surfaces allow Mariani to easily clean the ProBins, further reducing the risk of cross contamination compared to when they used wood. Processing an average of 900,000 pounds of fruit in about 1000 ProBin 24-S containers each day makes an easy-to-clean container extremely important.
Mariani is able to wash 480 ProBin 24-S in an 8 hour shift, greatly improving their processing efficiencies.
Increased Storage Capacity and Product Protection
ProBins are designed with an interlocking foot design and reinforced columns so that Mariani can stack ProBins higher, straighter, and in more secure columns than wood bins. ProBins also weigh less than wood bins, so they are easier to maneuver as well. Forklift traffic and the risk of falling containers have been reduced, which were both issues for Mariani when using wood bins.
Mariani can now stack 8 ProBin 24-S containers compared to previously stacking only 4 wood bins per column, doubling their storage capacity.
ProBins have always provided a safe product environment, but Mariani was in need of a new, more durable lid for even greater protection. Macro Plastics responded with the introduction of the MacroLid®in 2006. MacroLids are made with the same heavy-duty, injection-molded plastic as ProBins. They snap tightly to the ProBins for a secure fit, further reducing the risk of product contamination.